Feature by Ranjan Chatterjee, CIMETRIX
and Daniel Gamota, JABIL
Abstract
The vertical segments of the electronic products manufacturing industry (semiconductor, outsourced system assembly, and test, and PCB assembly) are converging, and service offerings are consolidating due to advanced technology adoption and market dynamics. The convergence will cause shifts in the flow of materials across the supply chain, as well as the introduction of equipment and processes across the segments. The ability to develop smart manufacturing and Industry 4.0 enabling technologies (e.g., big data analytics, artificial intelligence (AI), cloud/edge computing, robotics, automation, IoT) that can be deployed within and between the vertical segments is critical. The International Electronics Manufacturing Initiative (iNEMI) formed a Smart Manufacturing Technology Working Group (TWG) that included thought leaders from across the electronic products manufacturing industry. The TWG published a roadmap that included the situation analysis, critical gaps, and key needs to realize smart manufacturing.Article First Posted by SMT007 Magazine
Introduction
The future of manufacturing in the electronics industry is dependent on the ability to develop and deploy suites of technology platforms to realize smart manufacturing and Industry 4.0. Smart manufacturing technologies will improve efficiency, safety, and productivity by incorporating more data collection and analysis systems to create a virtual business model covering all aspects from supply chain to manufacturing to customer experience. The increased use of big data analytics and AI enables the collection of large volumes of data and the subsequent analysis more efficient. By integrating a portfolio of technologies, it has become possible to transition the complete product life cycle from supplier to customer into a virtual business model or cyber-physical model. Several industry reports project manufacturers will realize tens of billions of dollars in gains by 2022 after deploying smart manufacturing solutions. In an effort to facilitate the development and commercialization of the critical smart manufacturing building blocks (e.g., automation, machine learning, or ML, data communications, digital thread), several countries established innovation institutes and large R&D programs. These collaborative activities seek to develop technologies that will improve traceability and visualization, to enable realtime analytics for predictive process and machine control, and to build flexible, modular manufacturing equipment platforms for highmix, low-volume product assembly.
The vertical segments of the electronic products manufacturing industry (semiconductor (SEMI), outsourced system assembly, and test (OSAT), and printed circuit board assembly (PCBA) are converging, and service offerings are being consolidated. This occurrence is due to the acceleration of technology development and the market dynamics, providing industry members in specific vertical segments an opportunity to capture a greater percentage of the electronics industry’s total profit pool.
The convergence of the SEMI, OSAT, and PCBA segments will cause shifts in the flow of materials across the supply chain, as well as the introduction of equipment and processes across the segments (e.g., back-end OSAT services offered by PCBA segment). OSAT services providers are using equipment and platforms typically found in semiconductor back-end manufacturing, and PCBA services providers are installing equipment and developing processes similar to those used by OSAT.
The ability to develop smart manufacturing technologies (e.g., big data analytics, AI, cloud/ edge computing, robotics, automation, IoT) that can be deployed within the vertical segments as well as between the vertical segments is critical. In addition, the ability to enable the technologies to evolve unhindered is imperative to establish a robust integrated digital thread.
As the electronic products manufacturing supply chain continues to evolve and experience consolidation, shifts in the traditional flow of materials (e.g., sand to systems) will drive the need to adopt technologies that seamlessly interconnect all facets of manufacturing operations. The iNEMI Smart Manufacturing TWG published a roadmap that would provide insight into the situation analysis and key needs for the vertical segments and horizontal topics (Figure 1) [1].
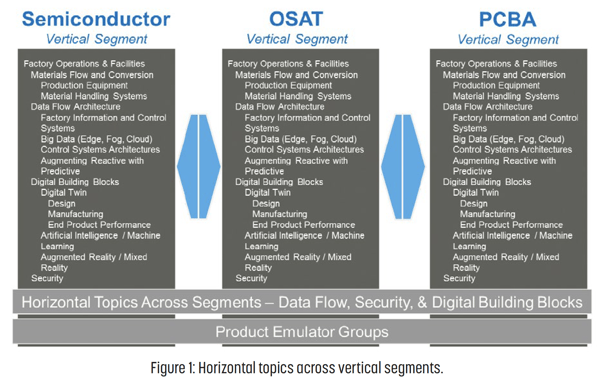
In this roadmap, the enabling smart manufacturing technologies are referred to as horizontal topics that span across the electronics industry manufacturing segments: security, data flow architecture, and digital building blocks (AI, ML, and digital twin).
The three electronics manufacturing industry segments SEMI, OSAT, and PCBA share some common challenges:•
- Responding to rapidly changing, complex business requirements
- Managing increasing factory complexity
- Achieving financial growth targets while margins are declining
- Meeting factory and equipment reliability, capability, productivity, and cost requirements
- Leveraging factory integration technologies across industry segment boundaries
- Meeting the flexibility, extendibility, and scalability needs of a leading-edge factory
- Increasing global restrictions on environmental issues
These challenges are increasing the demand to deploy, enabling smart manufacturing solutions that can be leveraged across the verticals.
Enabling Smart Manufacturing Technologies (Horizontal Topics): Situation Analysis
Many of the challenges may be addressed by several enabling smart manufacturing technologies (horizontal topics) that span across the electronics industry manufacturing segments: security, data flow, and digital building blocks. The key needs for these are discussed as related to the different vertical segments (SEMI, OSAT, and PCBA) and the intersection between the vertical segments.
Members of the smart manufacturing TWG presented the attribute needs for the following: security, data flow, digital building blocks, and digital twin. Common across the vertical segments is the ability to develop and deploy the appropriate solutions that allow the ability to manufacture products at low cost and high volume. Smart manufacturing is considered a journey that will require hyper-focus to ensure the appropriate technology foundation is established. The enabling horizontal topics are the ones that are considered the most important to build a strong, agile, and scalable foundation.
Security Security is discussed in terms of two classes: physical and digital. The tools and protocols deployed for security is an increasingly important topic that spans across many industries and is not specific only to the electronics manufacturing industry. Security is meant to protect a number of important assets and system attributes that may vary according to the process (novel and strong competitive advantage) and perceived intrinsic value of the intellectual property (IP).
In some instances, it directly addresses the safety of workers, equipment, and the manufacturing process. In other cases, it transitions toward the protection of electronic asset forms, such as design documents, bill of materials, process, business data, and others. A few key considerations for security are access control [2], data control [3], input validation, process confidentiality, and system integrity [2].
At the moment in manufacturing, in general, IT security issues are often only raised reactively once the development process is over and specific security-related problems have already occurred. However, such belated implementation of security solutions is both costly and also often fails to deliver a reliable solution to the relevant problem. Consequently, it is deemed necessary to take a comprehensive approach as a process, including implementation of security threat identification and risk analysis and mitigation cycles on security challenges.
Data Flow
General factory operations and manufacturing technologies (i.e., process, test, and inspection) and the supporting hardware and software are evolving quickly; the ability to transmit and store increasing volume of data for analytics (AI, ML, predictive) is accelerating. Also, the advent and subsequent growth of big data are occurring faster than originally anticipated. This trend will continue highlighting existing challenges and introducing new gaps that were not considered previously (Figure 2).
As an example, data retention practices must quickly evolve; it has been determined that limitations on data transmission volume and length of data storage archives will disappear (e.g., historical data retention of “all” will become standard practice). Examples of data flow key considerations are data pipes, machine-tomachine (M2M) communication, and synchronous/ asynchronous data transmission.
A flexible, secure, and redundant architecture for data flow and the option considerations (e.g., cloud, fog, versus edge) must be articulated. The benefits and risks must be identified and discussed. Data flow and its ability to accelerate the evolution of big data technologies will enable the deployment of solutions to realize benefits from increases in data generation, storage, and usage. These capabilities delivering higher data volumes at real-time and nearreal- time rates will increase the availability of equipment parameter data to positively impact yield and quality. There are several challenges and potential solutions associated with the increases in data generation, storage, and usage; capabilities for higher data rates; and additional equipment parameter data availability.
The primary topics to address are data quality and incorporating subject-matter expertise in analytics to realizing effective on-line manufacturing solutions. The emergence of big data in electronics manufacturing operations should be discussed in terms of the “5 Vs Framework”:
- Volume
- Velocity
- Variety (or data merging)
- Veracity (or data quality)
- Value (or application of analytics)
The “5 Vs” are foundational to appreciate the widespread adoption of big data analytics in the electronics industry. It is critical to address the identified gaps—such as accuracy, completeness, context richness, availability, and archival length—to improve data quality to support the electronics manufacturing industry advanced analytics [4].
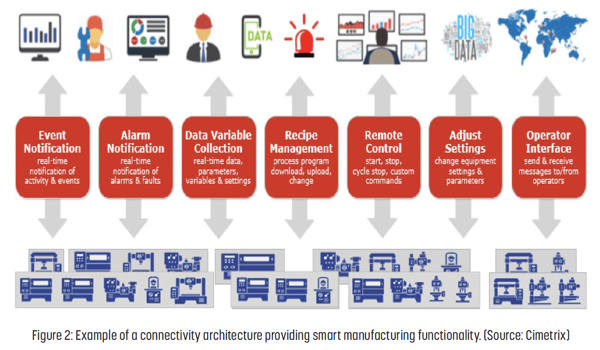
Digital Building Blocks
The advancements in the development of digital building blocks (interconnected digital technologies) are providing digitization, integration, and automation opportunities to realize smart manufacturing benefits. These technologies will enable electronics manufacturing companies to stay relevant as the era of the digitally- connected smart infrastructure is developed and deployed. Several technologies considered fundamental digital building blocks are receiving increased attention in the electronics manufacturing industry (e.g., AI, ML, augmented reality, virtual reality, and digital twin).
AI and ML
AI and ML tools and algorithms can provide improvements in production yields and quality. These tools and algorithms will enable the transformation of traditional processes and manufacturing platforms (processes, equipment, and tools). The situation analysis for AI and ML, as well as their enablers, typically consider the following features and operational specifications: communications at fixed frequency, commonality analysis, material and shipment history and traceability, models for predicting yield and performance, predefined image processing algorithms, secure gateway, warehouse management systems.
AI and ML present several opportunities to aggregate data for the purpose of generating actionable insights into standard processes. These include, but are not limited to, the following:
- Preventive maintenance: Collecting historical data on machine performance to develop a baseline set of characteristics on optimal machine performance, and to identify anomalies as they occur.
- Production forecasting: Leveraging trends over time on production output versus customer demand, to more accurately plan production cycles.
- Quality control: Inspection applications can leverage many variants of ML to fine-tune ideal inspection criteria. Leveraging deep learning, convolutional neural networks, and other methods can generate reliable inspection results, with little to no human intervention.
- Communication: It is important for members of the electronics manufacturing industry to adopt open communication protocols and standards [5–8].
Digital Twin Technology
The concept of real-time simulation is often referred to as the digital twin. Its full implementation is expected to become a requirement to remain cost-competitive in legacy and new facility types. Digital twin will initially be used to enable prediction capabilities for tools and process platforms that historically cause the largest and most impactful bottlenecks. The ultimate value of the digital twin will depend on its ability to continue to evolve by ingesting data and the availability of data with the “5 Vs”: veracity, variety, volume, velocity, and value. The situation analysis of the digital twin within and between electronics industry manufacturing segments highlight the following data considerations: historical, periodic, and reactive.
The concept of a digital twin lends itself to on-demand access, monitoring and end-toend visualization of production, and the product lifecycle. By simulating production floors, a factory will be able to assess attainable projected KPIs (and what changes are required to attain them), forecast production outputs, and throughputs through a mix of cyber-physical realities (the physical world to the virtual world, and back to the physical world), and expedite the deployment of personnel and equipment to manufacturing floors worldwide.
Enabling Smart Manufacturing Technologies (Horizontal Topics): Key Attribute Needs
Security
Security will continue to be a primary concern as the electronics manufacturing industry adopts technologies and tools that rely on ingested data to improve manufacturing quality and yield and offer differentiated products at a lower cost and higher performance. SEMI members generated a survey to appreciate the needs, challenges, and potential solutions for security in the industry and its supply chain and gather more comprehensive input from the industry in terms of users, equipment and system suppliers, security experts, and security solution providers [9]. It is a topic that permeates many facets of manufacturing: equipment, tools, designs, process guidelines, materials, etc. Processes continue to demand a significant level of security to minimize valuable know-how IP loss; this requirement will generate the greatest amount of discussion such as data partitioning, production recipes, equipment, and tool layout. A few key attribute needs for security are network segmentation [10], physical access, and vulnerability mitigation.
These security issues are not unique to microelectronics manufacturing, and many of the issues go beyond manufacturing in general. The topic of security should reference the challenges and potential solutions across the manufacturing space. As an example, the IEC established an Advisory Committee on Information Security and Data Privacy [11figuredfdafdfd. It is suggested to collaborate with other standards and industry organizations that are developing general manufacturing security roadmaps by delineating specific microelectronics manufacturing issues and focusing on common needs.
Data Flow
The development of a scalable architecture that provides flexibility to expand; connect across the edge, the fog, and the cloud; and integrate a variety of devices and systems generating data flow streams is critical. A smart factory architecture may, for example, accommodate the different verticals in the electronics manufacturing industry as well as companies in non-electronics manufacturing industries.
As mentioned previously, different industries seeking to deploy smart manufacturing technologies should leverage architectures thatprovide the desired attributes; data flow architecture is considered a prime candidate for leveraging and cross-industry collaboration to identify optimum solutions (i.e., data synchronizers, execution clients).
The development and deployment of technologies for data flow are accelerating. Focus on data analytics, and data retention protocols are increasing at a faster rate than first anticipated. It is imperative to collect the critical data as well as to establish guidelines to perform intelligent analysis and to exercise the appropriate algorithms to specify data-driven decisions. Several topics related to data are under consideration, such as general protocols:
- “All” versus “anomaly” data retention practices
- Optimization of data storage volumes
- Data format guidelines for analytics to drive reactive and predictive technologies
- Data quality protocols enabling improvements in time synchronization, compression/uncompression, and blending/merging
- Guidelines to optimize data collecting, transferring, storing, and analyzing
Data considerations for equipment are:
- Defining context data sets for equipment visibility
- Improving data accessibility to support functions
- Data-enabled transition from reactive to redictive functionality
- Data visibility of equipment information (state, health, etc.)
Digital Building Blocks
The ability to deploy the necessary digital building blocks to realize smart manufacturing is at different stages of maturity.
AI and ML
A few key attribute needs for AI and ML are data communication standards, data formatting standards, and 3PL tracking solutions. Technologies, such as AI and ML, are seen as enablers to transition to a predictive mode of operation: predictive maintenance, equipment health monitoring, fault prediction, predictive scheduling, and yield prediction and feedback. This paradigm in AI-enhanced control systems architectures will enable the systems to “learn” from their environment by ingesting and analyzing large data sets. Advanced learning techniques will be developed that improve adaptive model- based control systems and predictive control systems. The continued development and assessment of AI and ML technologies is critical to establish the most robust and well-tuned prediction engines that are required to support emerging production equipment.
Digital Twin Technology
Advances in digital twin technologies are accelerating as the potential benefits are communicated to end-users. Also, the costs for enabling technologies (hardware and software platforms) are becoming less expensive. The following are considered key attribute needs that will increase adoption and broad-based deployment of the digital twin (product design, product manufacturing, and product performance: digital thread, predictive, prescriptive, and systemwide continuous data access.
Digital twin is a long-term vision that will depend on the implementation of discrete prediction capabilities (devices, tools, and algorithms) that are subsequently integrated on a common prediction platform. It is generally considered that the digital twin will provide a real-time simulation of facility operations as an extension of the facility operations system.
The successful deployment of digital twin in a facility environment will require high-quality data (e.g., accuracy, velocity, dynamic updating) to ensure the digital twin is an accurate representation of the real-time state of the fab. Also, the realization of this vision will depend on the ability to design an architecture that provides the key technologies to operate collaboratively by sharing data and capabilities. Ultimately, the success of the digital twin will depend on the ability to develop a path for implementation that provides redundancy and several risk assessment gates.
Prioritized Research, Development, and Implementation Needs
The topic of collaboration is often mentioned in industry-led initiatives as a key element to realize the benefits attributed to smart manufacturing. There is a strong drive by members of the electronics manufacturing industry to engage in activities that foster collaboration. Participants in these activities recognize that solutions must be consensus-based and adopted by many vendors. Equipment suppliers appreciate that deep domain knowledge combined with data analysis contributes to only a fraction of the potential value that can be captured. The optimal value will be realized when data is shared across manufacturing lines in facilities, with vertical segment industry supply chain members and across vertical segments.
Example prioritized research, development, and implementation needs topics are as follows:
- Define data flow standard interfaces and data formats for all equipment and tools
- Investigate if data flow continuity between vertical segments should be mandatory or optional
- Determine optimal operation window for the latency of data versus process flow and quantify permissible latency for data flow when used to determine process go/no-go
- Investigate data security and encryption requirements when sharing common process tools versus isolating process equipment between vertical segments
- Develop open and common cross-vertical-segments communication standards and protocols for equipment
Gaps and Showstoppers
There is universal agreement that digitization will drive huge growth in data volumes. Many predict that cloud and hybrid cloud solutions are critical to enable the storage and subsequent manipulation of data by AI algorithms to derive value. However, industry members must adopt consensus-based standards and guidelines for connectivity protocols and data structures (Figure 4). Smart manufacturing is a journey, and a robust and scalable connectivity architecture must be established on which to deploy digital building blocks (e.g., AI, ML to extract the optimal value from the data).
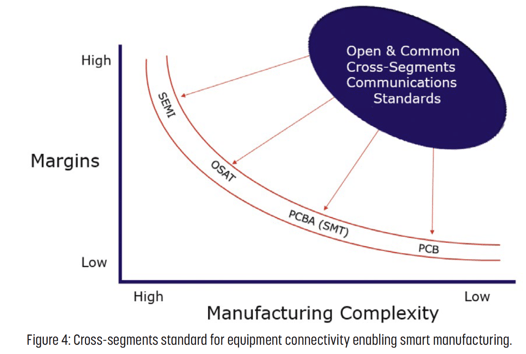
Example critical gaps that could significantly impact the progress of the deployment and adoption of smart manufacturing are:
- Undefined data security between vertical segments
- Lack of machine interface standardization for data flow
- Undefined data formats for data flow
- Data vulnerability when security is breached
- Robust and scalable connectivity architecture across electronics vertical segments to enabling smart manufacturing functionality (event and alarm notification, data variable collection, recipe management, remote control, adjustment of settings, interfacing with operators, etc.)
Summary
The iNEMI Smart Manufacturing Roadmap Chapter provides the situation analysis and key attribute needs for the horizontal topics within the vertical segments as well as between the vertical segments. Also, the chapter identifies the primary gaps and needs for the horizontal topics that must be addressed to enable the realization of smart manufacturing:
- Definitions: Smart manufacturing, smart factory, Industry 4.0, AI, ML, etc.
- Audits for smart manufacturing readiness: Develop consensus-based documentation, leverage published documents (e.g., Singapore Readiness Index [12])
- Security: Best practices, physical, digital, local and remote access, etc.
- Equipment diversity and data flow communications: Old, new, and mixture
- Data attribute categorization and prioritization: Volume, velocity, variety, veracity, and value
- Cost versus risk profile versus ROI
- Talent pool (subject-matter experts): Data and computer scientists, manufacturing engineers, and automation
- Standards and guidelines: Data formats and structures, communication protocols, and data retention
- Open collaboration: SEMATECH 2.0
The gaps and needs that were identified for addressing require additional detail for the status of the different vertical segments to appropriately structure the initiatives. It was suggested to circulate surveys to gather the information to appreciate the issue. One survey format was suggested as an example template: Manufacturing Data Security Survey for IRDS FI Roadmap [13].
iNEMI, together with other organizations, such as SEMI, can organize workshops to facilitate collaboration between the electronics manufacturing industry stakeholders. In addition, iNEMI can establish cross-industry collaborative projects that can develop the enabling technologies to address the roadmap identified needs and gaps to realize smart manufacturing.
Further, organizations, such as iNEMI and SEMI, can collaborate to establish guidelines and standards (e.g., data flow interfaces and data formats) as well as lead groups to develop standards for equipment and tool hardware to reduce complexity during manufacturing. Also, iNEMI can engage other industry groups to foster the exchange of best practices and key knowledge from smart manufacturing initiatives.
The members of the roadmap TWG are committed to provide guidance during the smart manufacturing journey—people, processes, and technologies. Members of the TWG also suggested engaging microelectronics groups as well as non-microelectronics groups to assess opportunities to leverage existing smart manufacturing guidelines and standards.
Acknowledgments
Thank you to the members of the iNEMI Smart Manufacturing TWG. Their dedication, thought leadership, and deep appreciation for SMT enabling technologies was critical to preparing the roadmap chapter.
In addition, we would like to thank the participants and facilitators of the SEMI Smart Manufacturing Workshop—Practical Implementations and Applications of Smart Manufacturing (Milpitas, California, on November 27, 2018). SMT007
References
1. 2019 iNEMI Roadmap.
2. U.S. National Institute Standard and Technology’s Special Publication 800-82.
3. U.S. National Institute Standard and Technology’s Special Publication 800-171.
4. IEEE International Roadmap for Devices and Systems, Factory Integration.
5. Japan Robot Association’s Standard No. 1014.
6. SEMI E30-0418, Generic Model for Communications and Control of Manufacturing Equipment (GEM); SEMI A1-0918 Horizontal Communication Between Equipment; SEMI E5-1217, Communications Standard 2 Message Content (SECS-II); SEMI E4-0418, Equipment Communications Standard 1 Message Transfer (SECS-I).
7. Hermes Standard.
8. IPC-CFX Standard.
9. J. Moyne, S. Mashiro, and D. Gross, “Determining a Security Roadmap for the Microelectronics Industry,” 29th Annual SEMI Advanced Semiconductor Manufacturing Conference (ASMC), pp. 291–294, 2018.
10. IEC 62443 3-2.
11. website: iec.ch/acsec.
12. EDB Singapore, “The Singapore Smart Industry Readiness Index,” October 22, 2019.
13. www.surveymonkey.com/r/ZXLS6LH.
Ranjan Chatterjee is vice president and general manager, smart factory business, at Cimetrix.
Dan Gamota is vice president, manufacturing technology and innovation, at Jabil.
Article First Posted by SMT007 Magazine
Feature by Ranjan Chatterjee, CIMETRIX
and Daniel Gamota, JABIL
Editor’s note: Originally titled, “The Convergence of Technologies and Standards Across the Electronic Products Manufacturing Industry (SEMI, OSAT, and PCBA) to Realize Smart Manufacturing ” this article was published as a paper in the Proceedings of the SMTA Pan Pacific Microelectronics Symposium and is pending publication in the IEEE Xplore Digital Library.