Purpose of Spooling Messages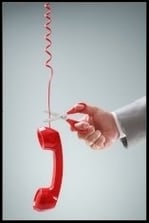
Even the most robust computer networks experience communication failure. Regardless of the cause, a small outage could be responsible for a significant amount of mission critical data loss. GEM mediates this loss of data by providing the message spooling capability.
Spooling Definition
“Spooling is a capability whereby the equipment can queue messages intended for the host during times of communication failure and subsequently deliver these messages when communication is restored" SEMI E30-0717 7.12.
Spooling Benefits
Automated factories are data-driven. Data is extracted and analyzed to make decisions that influence how engineering and management teams react to ensure product yield is high and scrap is low.
Gaps in this data could lead to erroneous judgement or even guessing. Spooling is a backup system that ensures this data will be preserved and restored reducing the risk of losing valuable data.
GEM Capability Requirements
Spooling is not a GEM requirement however, if this additional capability is implemented it must be done so properly. Here are a few requirements for implementing a compliant spooling interface.
The equipment must provide the host with the ability to enable and disable spooling via the equipment constant “EnableSpooling”. This EC is published by the equipment and the host can select the desired state.
When Spooling is implemented, it must be functional for all relevant primary messages and accessible using an S2, F43/F44 transaction. This excludes stream 1 messages which must be rejected if they attempt to “set spool”.
Non-Volatile Storage
The equipment is responsible for allocating enough non-volatile-storage to store all messages that have been spooled for at least one processing cycle of the equipment. The NVS will also house all spooling-related status variables. NVS is used for this data so that if a power outage occurs the data is persisted.
Loss of Power
All messages that were spooled prior to the equipment’s power loss will be available since they are persisted in non-volatile storage. All spooling context is restored from NVS if spooling was active at the time of the power loss occurred. This includes the spooled data as well as all spooling related status variables persisted in NVS.
Host responsibility for implementation of Spooling
Message spooling requires hosts to participate to successfully recover after a loss of communication. It is Ideal to leave spooling in the disabled state until the host has been programmed to properly handle all conditions that may occur in the entirety of this state machine. Disabled spooling is better than improperly managed spooling.
Once communication is re-established, the host must manage requesting the spooled messages. The host also has the option of purging the files from the equipment when necessary.
Conclusion
Though spooling is not a fundamental GEM requirement, if implemented it must be done so properly. Both host and equipment software have a responsibility to ensure GEM compliance when spooling is enabled. GEM spooling protects the potential loss of valuable data and provides a standard for both equipment and host software to adhere to with ease.
Click here to read the other articles in our SECS/GEM Features and Benefits series.
To download a white paper on an introduction to SECS/GEM, Click below: