The 2015 SEMICON Taiwan was held at the Taipei Nangang Exhibition Center in the Nangang District of Taipei City, Taiwan September 2-4. The event drew over 30,000 visitors from all over the world for the three-day event with nearly 1,500 exhibits from a diverse array of companies and organizations across the semiconductor industry.
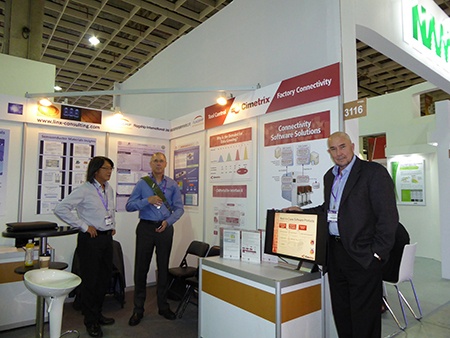

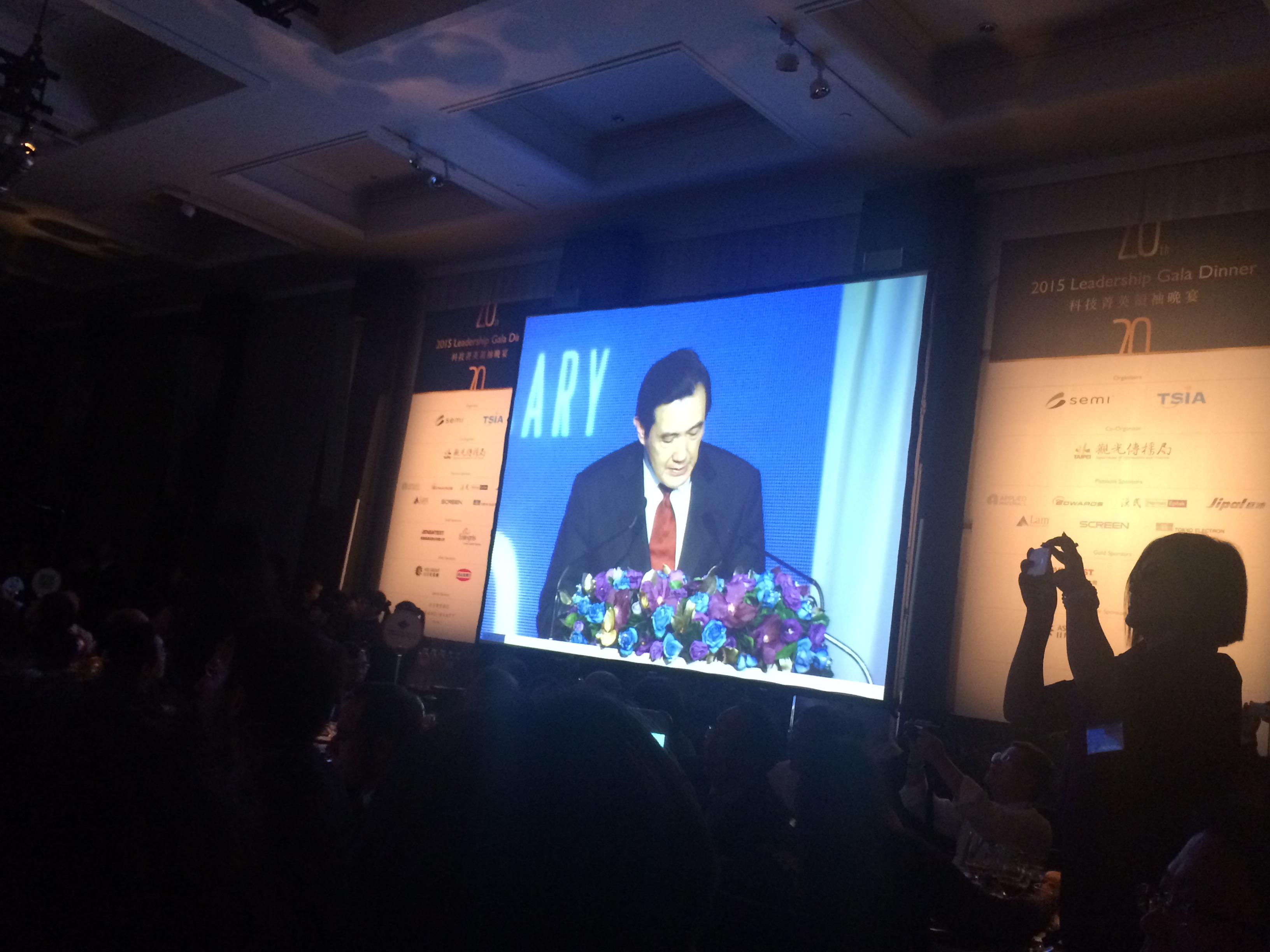
Cimetrix exhibited at SEMICON Taiwan trade show for the first time, in conjunction with its newest Asian partner, Flagship International.
This turned out to be the 20th Anniversary of SEMICON Taiwan, so the mood was especially buoyant and the attendance brisk. SEMI also commemorated the event with a Gala Dinner at the Grand Hyatt on Wednesday night, and we were privileged to attend courtesy of our Flagship colleagues.
The president of Taiwan, Ma Ying-jeou, even made a guest appearance to thank the semiconductor industry for its contribution to Taiwan’s economic health.
Shortly after the exhibition opened on Wednesday (Sept. 2), a couple of visitors from UMC showed up, and shared the latest work they’ve been doing with the Wait Time Waste (WTW) concepts that we had presented two years earlier. C.Y. Tiao and James Lin of UMC even made two presentations at the eMDC conference on this topic.
From a standards perspective, this has now taken the form of SEMI E168, Specification for Product Time Measurement (PTM), and has been defined at the “time element” and supporting GEM/SECS message level for process equipment, automated material handling systems (AMHS), and material control systems (MCS). With the advent of SEMI E164 (EDA Common Metadata), these concepts are especially easy to implement, because all the events necessary to calculate the full suite of time elements are required by standard… but more on this is a later blog!
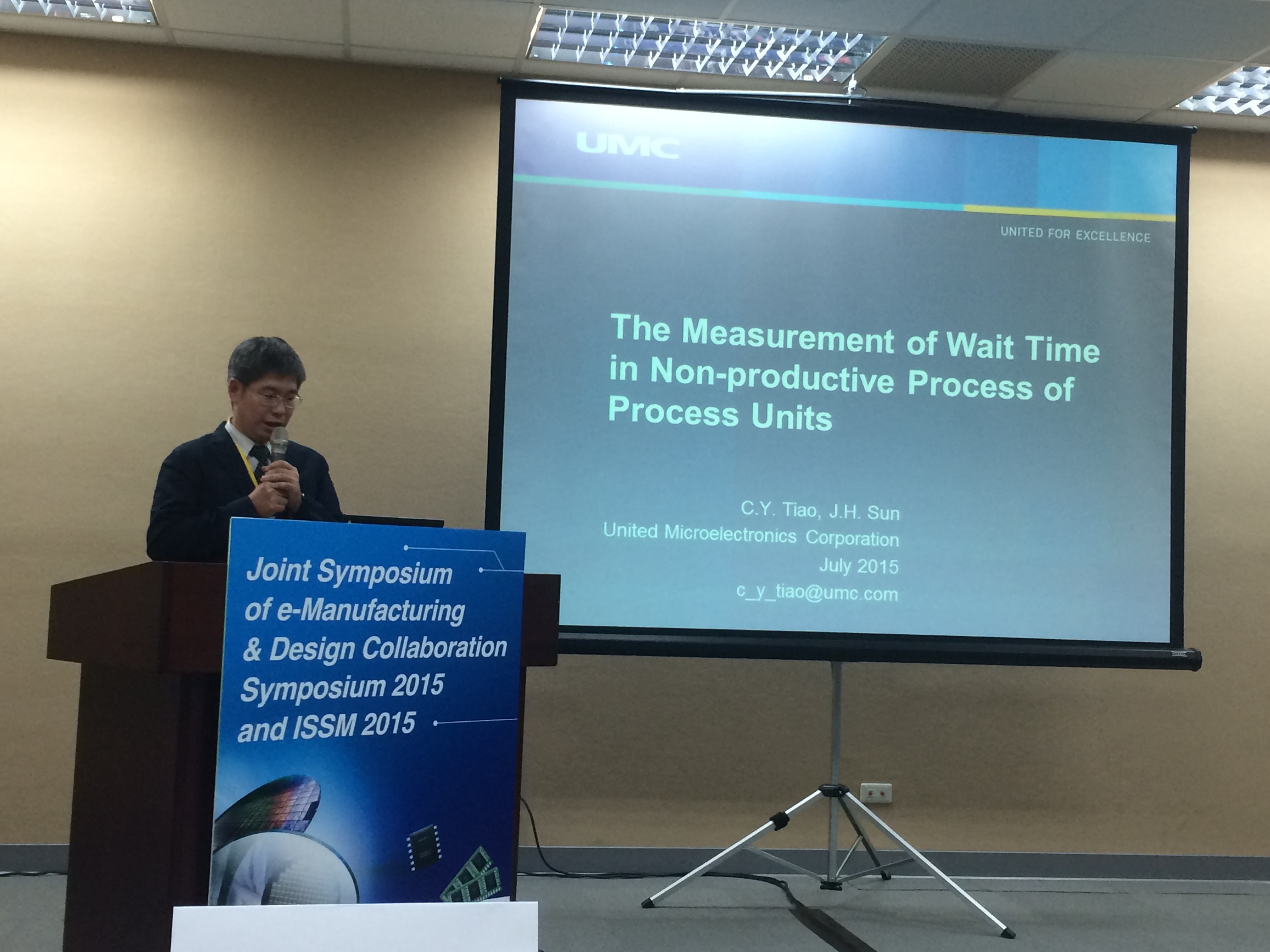
Since much of the world’s foundry capacity is in Taiwan, the equipment industry was well represented at the show, which included many of Cimetrix’ current customers as well as a few local prospects. As a result, Dave Faulkner and Kerry Iwamoto had a chance to visit a number of these firsthand.
Another highlight of the week for Cimetrix was participation in the eMDC (e-Manufacturing & Design Collaboration Symposium), where I made a presentation entitled “Data Fusion at the Source: Standards and Technologies for Seamless Sensor Integration” that addresses the challenges faced by process engineers in effectively using data from an increasing number of sources to analyze process behavior.
The basic idea is to handle the association of necessary context information (lot, substrate, product, layer, process, recipe, step, chamber, etc.) with the raw collected data as close to the source as possible, using a single, integrated model of the equipment and all related data sources. The equipment model that forms the foundation of the EDA/Interface A standards serves this purpose perfectly.
On a final related note, in visiting and talking with a number of the leading chip makers during the week, it seems that the adoption momentum for EDA is now building steadily, so we look forward to supporting this initiative across the value chain. Stay tuned for a late September post that will shed more light on this process!